T800 - Bearing Manufacturing Facility
Application of T800 Series Space Logistics Truss Robot
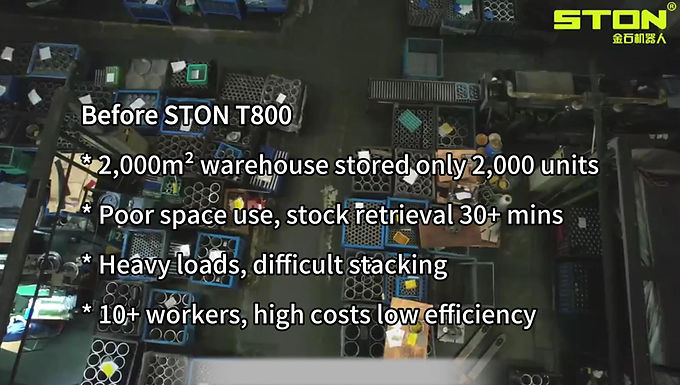
Before the implementation of the STON T800, the client’s warehouse operations were inefficient, with poor space utilisation and a disorganised storage system. In the 2,000m² warehouse, only 2,000 units could be stored, and locating stock took over 30 minutes due to cluttered inventory placement. The heavy loads made multi-layer stacking challenging, requiring more than 10 workers to manage daily operations, resulting in high labour costs and low efficiency.
Since adopting the STON T800, storage capacity has been significantly improved. The high-density stacking system maximises space utilisation, enabling the same 2,000m² warehouse to store 5,000 units—an increase of 2.5 times—greatly alleviating storage pressures.
Outbound efficiency has also seen a remarkable 30-fold improvement compared to manual operations. Previously, workers manually located and moved stock, a time-consuming and labour-intensive process. With the automated system, inventory is precisely tracked and retrieved, streamlining outbound processes and minimising manual handling time.
Labour costs have decreased substantially, with the warehouse now operating with just two staff members instead of over ten, reducing workforce expenses while enhancing overall efficiency. The T800’s intelligent warehouse management system automates inventory monitoring and scheduling, reducing errors and risks, ensuring accurate stock placement and retrieval, and improving safety and work quality—all while lowering operational costs.